A simple and comprehensive solution for deviation reporting and continuous improvements
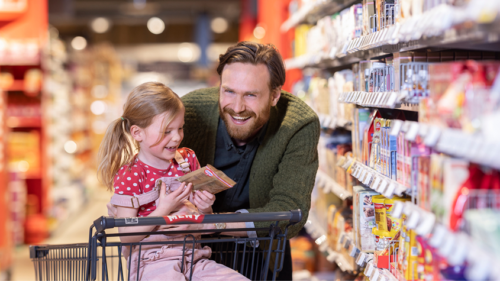
Input for operational development
All production deviations and deviations in areas such as cleaning, building technology, goods reception, IT, health, environment and safety, as well as deviations in warehouse automation, are reported in the quality control solution from IMI. All reported deviations and claims are automatically sent to the right person for assessment and rectification. The deviations can be of many different types, such as incorrect or damaged deliveries, temperature deviations or a warehouse door or truck that needs service.
“The greatest benefit of the system is that it has become so easy for staff to report deviations, which in turn means that large amounts of data can be collected, analyzed and provide us with input for our internal operational development and our dialogues with various suppliers.”
Our quality control solution is used by all ASKO staff who work with goods handling. From receipt of goods until the goods are delivered to the customers. The group’s drivers also use the system as an app on their mobile phones. With the help of the app, all deviations and claims related to operations, health, environment and safety can be reported easily and quickly.
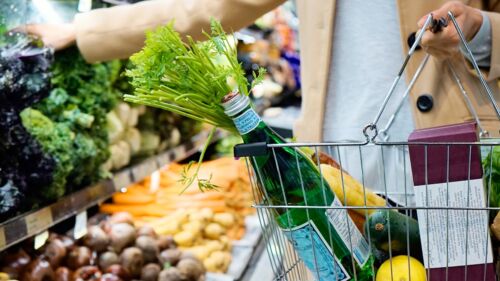
Close development collaboration
ASKO’s and IMI’s collaboration began in 2014 in conjunction with the construction of ASKO’s central warehouse for refrigerated goods in Vestby, Akershus. At the time, the project organization needed a system in which a multitude of planned activities could be gathered and monitored over the three-year period of construction. This was the starting point for development of the quality control solution from IMI – a system that in 2021 was rolled out at all ASKO regional subsidiaries and which is also used by several other market-leading companies, including Europris, the Haugen Group, and 4Service.
“Over the course of a year, our employees report approximately 36,000 events in the system. The goal moving forward is that we, together with IMI, will become even better at using all the data to conduct deeper analyses as a basis for work with improvements,” says Grethe and emphasizes the closeness of collaboration with IMI’s staff and that they work well together in further developing the system.
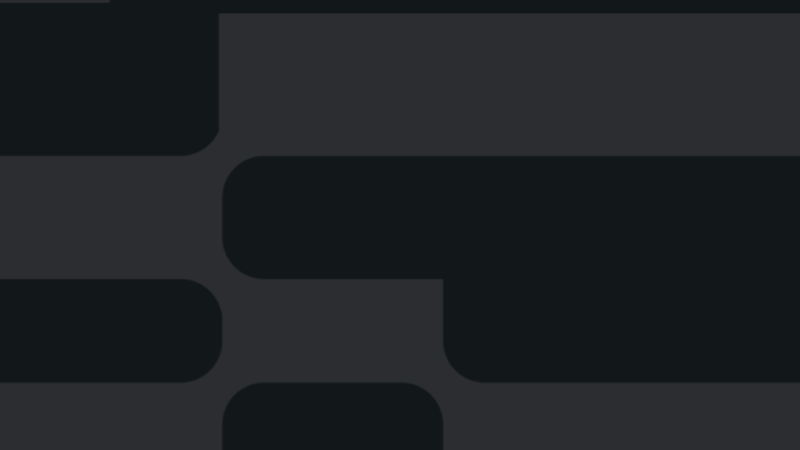