Stadium have quintupled its savings on return management, while everything continues to be handled within Sweden. By optimizing its processes, they have not only increased efficiency but also created a smoother experience for both customers and warehouse staff.
Standardization and digitization are key
Klas Hjort, returns researcher at Lund University, explains: “A few years ago, it became widely known that companies were sending their returns to the Baltics for processing, which sparked a major debate. He believes we should stop pointing fingers at e-commerce and instead highlight the good examples – where he believes Stadium is a company that has succeeded well – by standardizing the return process and digitizing the customer journey.” Stadium has Postnord TPL as their TPL partner at all three of its warehouses in Norrköping, and at the e-commerce warehouse, they have set up a return hub, which, along with digital solutions, has reduced the cost of handling a return to “under ten.”
“Previously, we had manual handling at our second warehouse, ‘Stadium DC’, where e-commerce was located before. The cost per handled return was very high, at 50 SEK, and that didn’t even include the shipping cost,” says Peter Carlson Hellqvist, supply chain development manager at Stadium.
This success is based on smart solutions that streamline the return flow, where our return system, together with inretrn, plays an important role in managing and simplifying the entire return process once the goods reach the warehouse.
Read the article from Dagens Logistik to learn more about how Stadium has succeeded with this and how the right system solutions can make a difference.
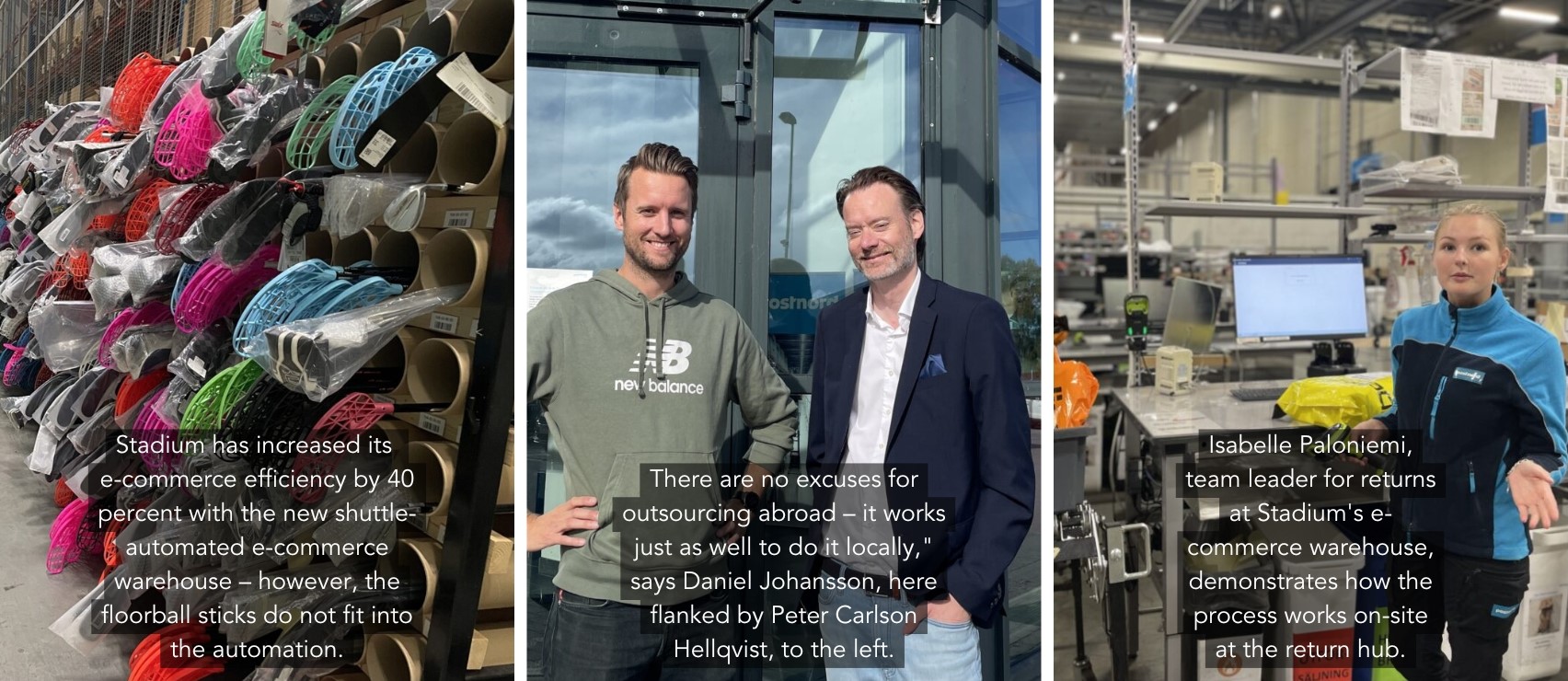
Text and image are sourced from Klara Eriksson, logistics journalist at Dagens Logistik.