For many years, transportation has been a top priority for cost-efficiency efforts within the logistics sector. This is due to its significant impact on company cost structures as well as on customer service levels. Estimates suggest that transportation costs can account for as much as 20 percent of a product’s total price. Because transportation has such a large influence on profitability and competitiveness, it is often in focus when companies seek to optimize their supply chains.
A Complex Area with Many Challenges
Transportation is, however, a complex cost area to manage, and several emerging trends are creating new challenges for trading companies, industrial enterprises, freight forwarders, and transport providers. In the coming years, we can expect increased road tolls, higher labor and operating costs, and new emissions charges imposed by EU regulations. Another trend is that many companies purchasing transport services are unwilling to absorb the rising costs faced by transport providers.
As a result, both “sides” of the market face different cost-related challenges. In this blog post, we aim to provide deeper insight into the importance of transportation costs for trade and industrial companies, explain some of the many factors affecting these costs, and offer advice for businesses looking to reduce their transportation expenses.
Transportation Can Account for Over Half of a Company’s Total Logistics Costs
For manufacturers, wholesalers, and retailers, transportation is often a major expense in the supply chain. In fact, it can account for more than 50% of a company’s total logistics costs, which also include warehousing, inventory handling, and administrative expenses.
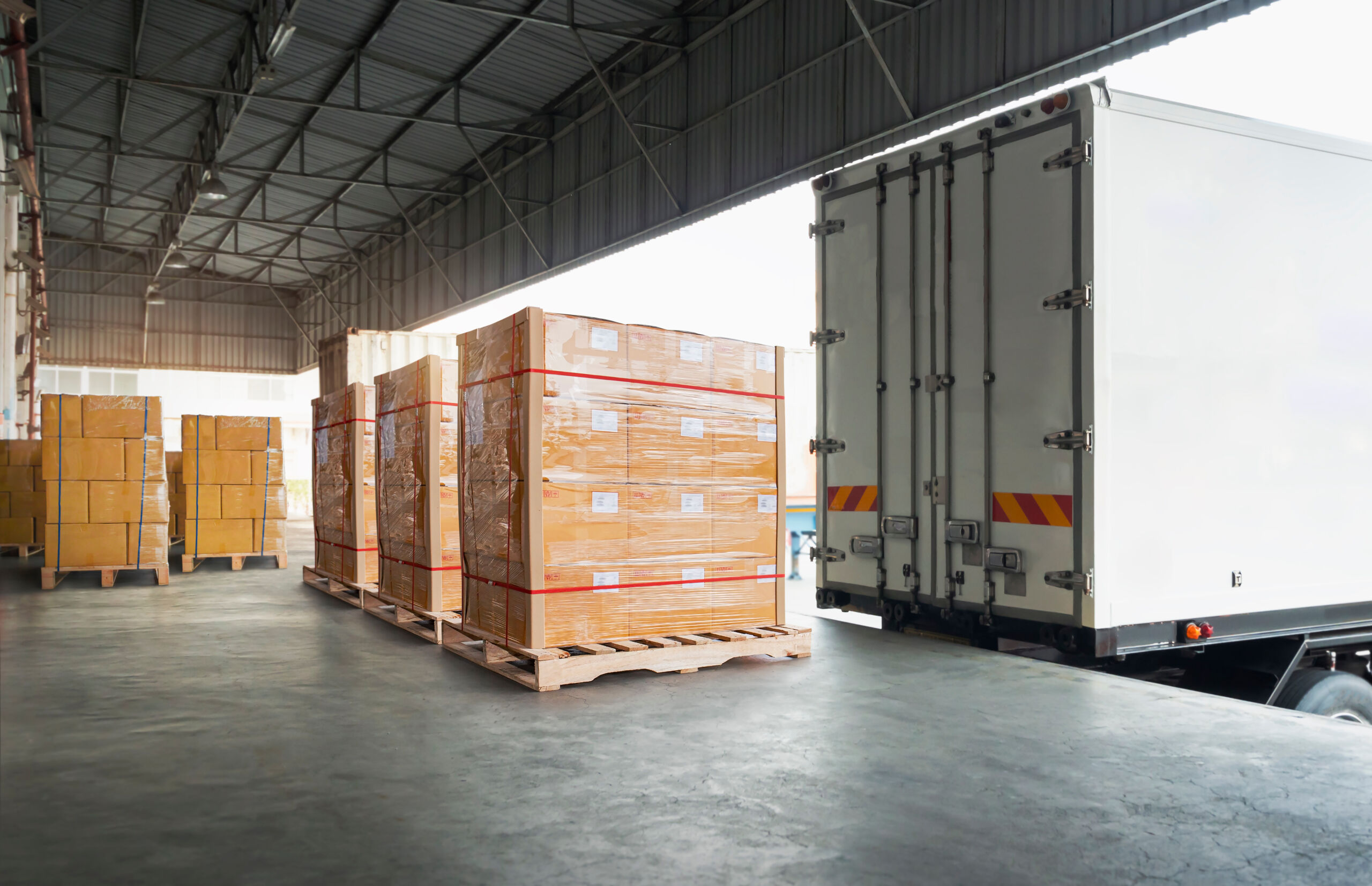
One driver of high transportation costs is the push by many companies to reduce inventory levels, which in turn requires more frequent deliveries. Other contributing factors to rising logistics costs include increased digitization, higher customer service expectations, the growth of e-commerce, deregulation, the geographical decentralization of production, and greater globalization of trade.
This evolution has led to a higher volume of transportation and a more complex cost structure. High transport costs have a direct impact on profitability, but they also present an opportunity for cost rationalization—provided companies gain a clear understanding of the factors behind these costs.
Industries Where Profitability, Margins, and Competitiveness Are Affected by High Transportation Costs
The construction sector is one example where rising transportation costs have translated into higher prices for end customers. Fuel prices have reached record highs worldwide, driving up costs for both local and international transport providers. These costs are typically passed along to customers, who in turn must adjust their product pricing. Rising raw material and energy costs have also played a key role in price increases in the construction industry.
In Sweden’s basic industries, transportation represents a large portion of the total product cost. Take forestry, for example—one of Sweden’s largest transportation buyers and exporters. Around 80% of its production is exported, and approximately 65% is shipped by sea. Due to long transport distances both domestically and internationally, transportation can make up about 20% of the product’s final price. The largest cost increases stem from new Swedish government-imposed charges (e.g., fairway dues), which are difficult to pass on to cost-sensitive customers in international markets.
Construction and forestry are just two examples of industries where transportation costs significantly impact margins, profitability, and competitiveness—especially when companies cannot pass those increased costs on to customers. This is also true in other sectors with high price pressure and limited flexibility to raise prices.
It Can Be Difficult to Get a Clear Overview of Total Costs
Getting a comprehensive view of transportation costs is a major challenge. One reason is that these costs often consist of numerous components, both direct and indirect. It may seem simple: goods are transported from point A to point B—how hard can it be to calculate the cost? In reality, it’s often much more complicated.
Decisions and events within the purchasing company can affect costs, and freight providers often use complex pricing models that include a variety of variables, such as fuel surcharges, tolls, and labor costs. Additional charges like customs duties, taxes, and special handling fees (e.g., for hazardous goods) further complicate the picture.
Why Do Transportation Cost Deviations Occur?
Accurately calculating transport costs can be difficult. One example comes from a large Swedish wholesaler whose cost models were based on forecasts that did not match actual costs. Their forecasts were based on estimated shipments from central warehouses to regional hubs, and then onward to end customers. Different freight providers had different pricing models—some with fixed costs, others with variable charges and surcharges.
Flaws in the cost model led to speculative assumptions about final prices, causing deviations from internal estimates that snowballed into significant year-end discrepancies. Due to high delivery volumes, it was not feasible to manually verify costs retroactively, as it would have resulted in excessive labor costs.
Another example is a Swedish forestry company with a highly complex transportation network. The company struggled to identify and track deviations in transportation costs, which caused issues in cost accruals. Transport made up more than ten percent of the company’s total costs, yet its planning system lacked the capability to provide a comprehensive overview. Both cases illustrate how inadequate system support can cause major problems when demands for cost control and deviation analysis increase.
Numerous Cost Components to Track in International Trade
Controlling transport costs is challenging even for companies operating only in Sweden—but becomes even more difficult with international trade. Export-related transportation costs may include domestic handling, international pickup, export customs clearance, freight charges, import customs clearance, foreign handling, and final delivery abroad.
Within Europe, transportation costs are typically governed by contractual terms between the shipper and freight provider. For shipments outside Europe, the amount of goods often determines the cost. The many cost components involved increase the need for robust, integrated systems.
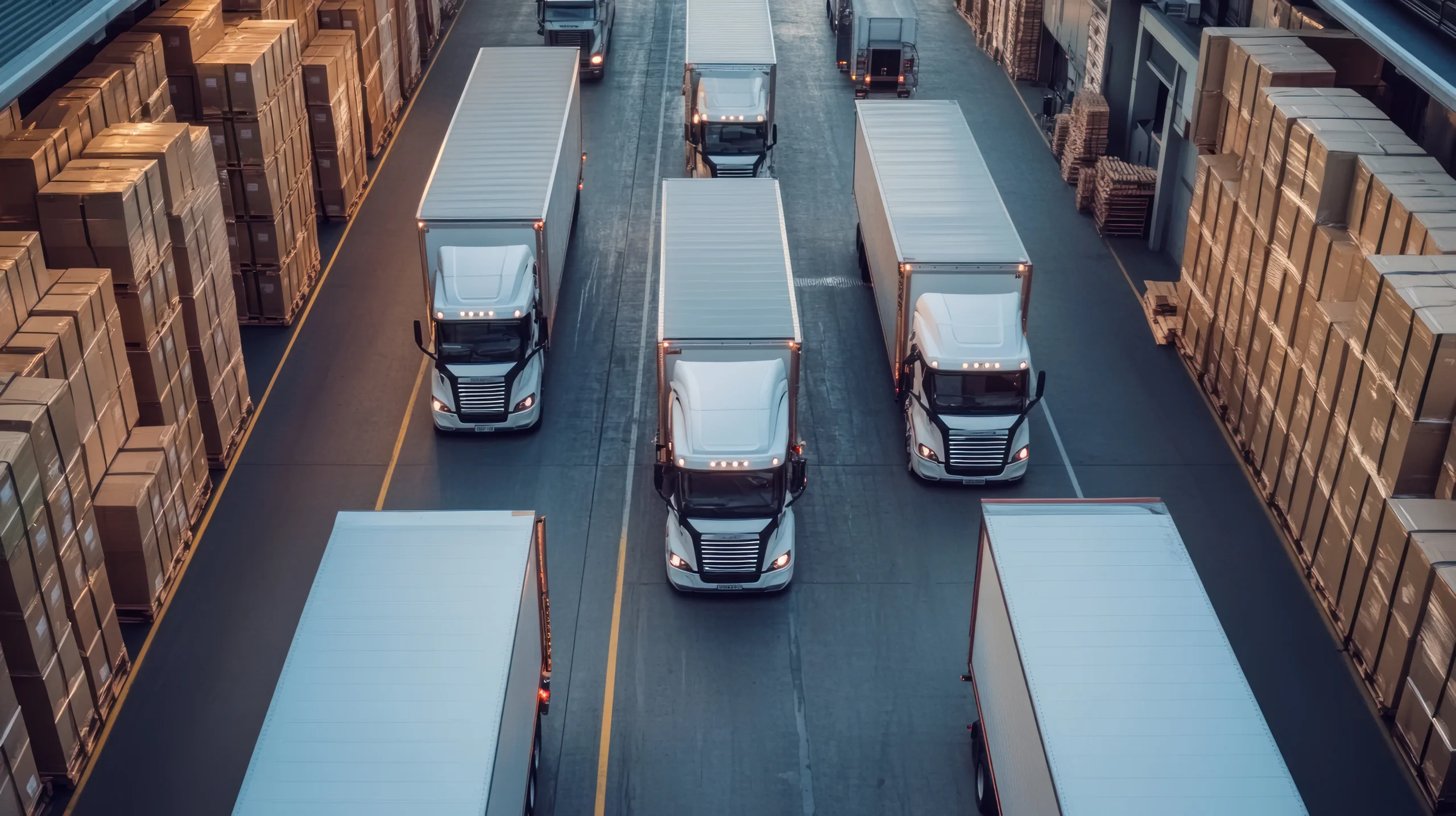
The Final Cost Is Influenced by Many Factors and Surcharges
Understanding the real transportation cost is further complicated by numerous influencing factors, fees, and surcharges. These include weight, volume, distance, fuel surcharges, oil prices, emission fees, shipment volume, urban area surcharges, pickup costs, notification fees, holiday capacity surcharges, customs duties, and taxes. If the goods are sensitive, difficult to handle, or of high value, costs for handling and insurance also increase. Freight providers use these variables to price services in a way that minimizes their own risk.
Most freight agreements specify a base rate, to which various surcharges are added. Companies with modern Transport Administration (TA) systems can estimate these in advance. However, unexpected charges can still arise—for example, due to incorrect weight or dimensions provided at booking, delivery obstacles, or incorrect shipment/contact information leading to re-delivery or storage.
For companies purchasing transport, understanding freight pricing is crucial since these costs represent a major supply chain expense. A lack of knowledge can lead to overpayment and significantly impact profitability.
Moreover, freight pricing can vary widely between providers and regions. Understanding how freight companies calculate rates helps companies negotiate better deals and avoid unexpected costs. A good practice is to thoroughly review freight terms and understand the variables that influence price.
Advice for a Manufacturing Company That Wanted to Reduce Transportation Costs
A few years ago, the University of Gothenburg conducted a case study of a Nordic manufacturing company. Despite market success, the company was struggling with high transportation costs—nearly 14% of total costs. The study aimed to answer two questions: How can the company create more cost-efficient transportation flows? And what can be done to reduce transportation expenses?
The company’s transportation setup was complex, with offices and warehouses across multiple countries. Management found it increasingly difficult to keep transportation costs at reasonable levels. Some of the
company’s transportation arrangements were based on long-standing contracts and fixed delivery schedules. The routines had not been reviewed for some time, and many decisions were made locally and manually.
The researchers behind the study identified several measures to help the company reduce transportation costs:
-
Consolidate Shipments: By bundling multiple smaller deliveries into fewer, larger shipments, the company could reduce the total number of transports and thereby cut costs.
-
Review Delivery Frequencies: The study recommended reducing the frequency of shipments to some customers—provided it did not compromise customer service—by optimizing delivery planning.
-
Switch to Cheaper Transport Modes: In some cases, switching from air freight to rail or sea freight was proposed, especially when delivery time was less critical.
-
Increase Load Utilization: Better planning and packaging could increase the fill rate of transport units, reducing cost per shipped unit.
-
Negotiate Better Contracts: Since several transport agreements had not been reviewed in a long time, the company was advised to renegotiate with current providers or invite new suppliers to bid.
-
Improve Internal Communication: Transport planning and procurement were handled by different departments. Better coordination could improve both strategic and operational cost control.
Transportation Costs Are a Complex But Crucial Piece of the Puzzle
To sum up, transportation costs are a crucial part of the logistics puzzle. For many companies—especially in manufacturing and trade—they make up a significant portion of total logistics expenses. However, because transportation is a complex and variable-heavy area, it is often difficult to get a clear picture of the true costs.
It is essential for companies to have reliable systems in place to monitor transportation costs and identify cost deviations early. Without such systems, there’s a high risk of cost increases that cannot be traced or corrected in time.
Five Practical Tips to Better Control Transportation Costs:
-
Map Your Total Costs: Understand what components your transportation costs include—both direct and indirect—and how they are structured.
-
Identify Cost Deviations: Implement systems and routines to regularly monitor deviations between expected and actual costs.
-
Review Your Freight Agreements: Ensure that freight pricing is clearly documented and understood—especially the variables that affect total cost.
-
Plan for Consolidation and Optimization: Analyze whether deliveries can be consolidated and whether your delivery frequencies or transport modes can be adjusted.
-
Improve Cross-Functional Collaboration: Ensure that purchasing, logistics, and finance departments are aligned on transportation strategy and cost control measures.
Transportation costs can seem like an uncontrollable expense—but with a structured approach, the right systems, and good internal collaboration, it is entirely possible to take back control.